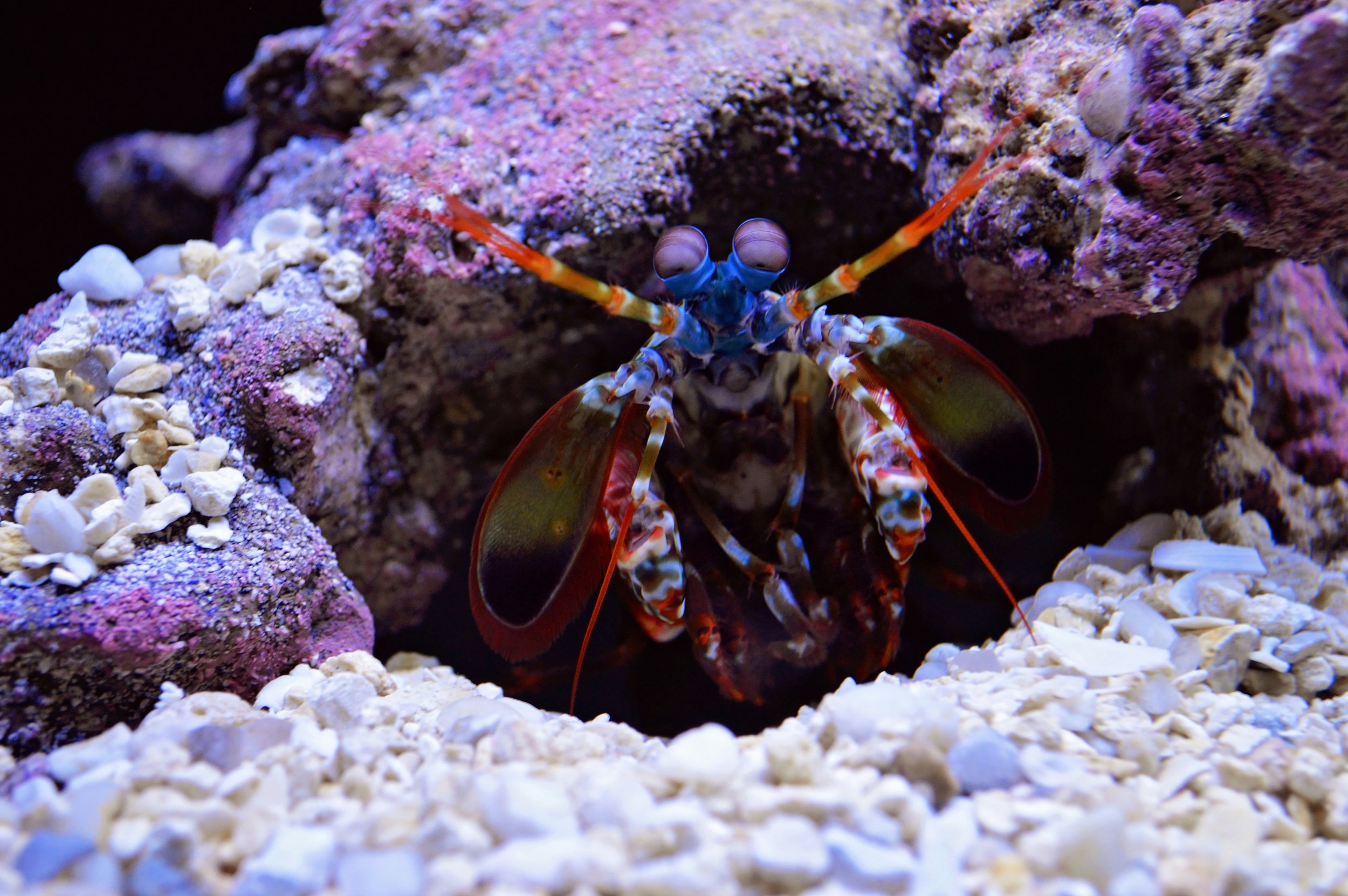
Helicoid-Inspired
Composites
Make it stand out.
-
Notched Bending & Other Properties
Notched bending tests performed on soft-polymer based helicoidal-inspired laminates show that decreasing the pitch angle leads to:
•a decreasing initiation value of fracture toughness; and
•a more stable, highly dissipative failure process characterized by a larger post-initiation load-bearing capability and delayed catastrophic failure
-
High-Velocity Impact Performance
Tailored helicoidal Carbon Fiber Reinforced Polymer (CFRP) laminates are capable of enhancing the high-velocity impact resistance over similar conventional cross-ply laminates which results in a +23% increase in the required perforation energy.
The balance between formation of matrix splits, helicoidal delaminations and fiber failure is key for the enhancement in high-velocity impact performance.
-
Quasi-Static Indentation
Reducing the pitch angle with ultra-thin-ply Carbon Fibre Reinforced Polymer (CFRP) helicoidal structures leads to a simultaneous increase in (i) maximum load-bearing capacity (92%), (ii) delay in catastrophic failure (74%) and (iii) energy dissipation (97%).
The capability of helicoidal structures of dissipating energy through the activation of several sub-critical mechanisms such as helicoidal distribution of delaminations and twisting matrix cracks, allows to overcome the inherent low performance to transverse loading of thin-ply CFRP (with standard lamination sequences).
-
Low-Velocity Impact & Compression After Impact
The best impact performing helicoidal configurations are capable of diffusing damage at sub-critical levels through the formation of matrix cracks, helicoidal delaminations and stable fibre failure.
Delaminations tend to be distributed helicoidally through-the-thickness of the laminate rather than being localised at a few ply interfaces.